Na Tehničkom fakultetu, Sveučilišta u Rijeci, održani su ONLINE otvoreni dani laboratorija. Članovi Laboratorija za precizno inženjerstvo doc. dr. sc. Ervin Kamenar, asistent Petar Gljušćić, mag. ing. mech. i asistent Tomislav Bazina, mag. ing. mech. uz vodstvo prof. dr. sc. Saše Zelenike, ukratko su predstavili neke od aktivnosti naše istraživačke skupine. Teme su bile: Napredne mjerne tehnike, sustavi za napajanje mreža osjetnika pomoću energije iz okoliša (engl. Energy Harvesting) te mehatronički sustavi za precizno pozicioniranje. Više detalja saznajete u priloženim snimkama!
Dani otvorenih laboratorija na RITEH-u
The Koopman Operator in Systems and Control
The book on “Koopman Operator in Systems and Control” is now available (electronic and hardcover versions). More information can be found and orders can be made on the webpage: Koopman Operator in Systems and Control .
The members of the Precenglab S. Zelenika and E. Kamenar together with I. Mezic from University of California, Santa Barbara (UCSB) and M. Korda from Centre national de la recherche scientifique (CNRS) authored the chapter “Application of Koopman-Based Control in Ultrahigh-Precision Positioning” (Pages 451-479).
Defense of the doctoral thesis – M. Perčić
On February 17th 2020, the doctoral thesis entitled “Characterization of Parameters Influencing Friction in the Nanometric Domain” was successfully defended by the member of the Centre for Micr-o and Nanosciences and Technologies, where the experimental part of the research was conducted.
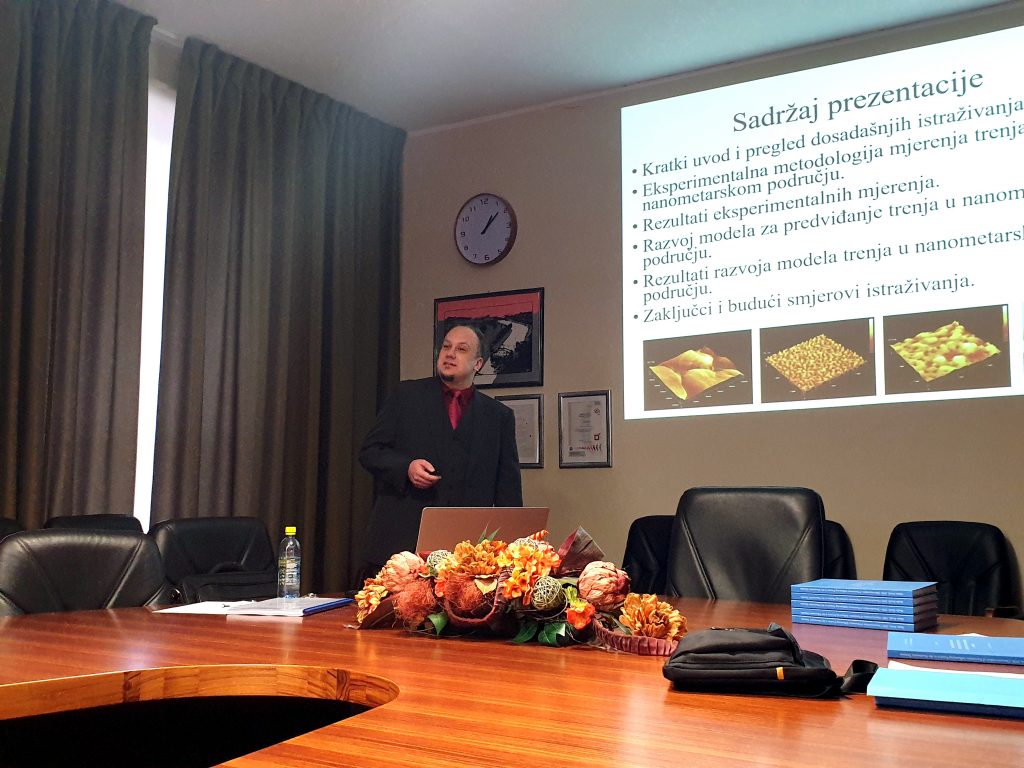
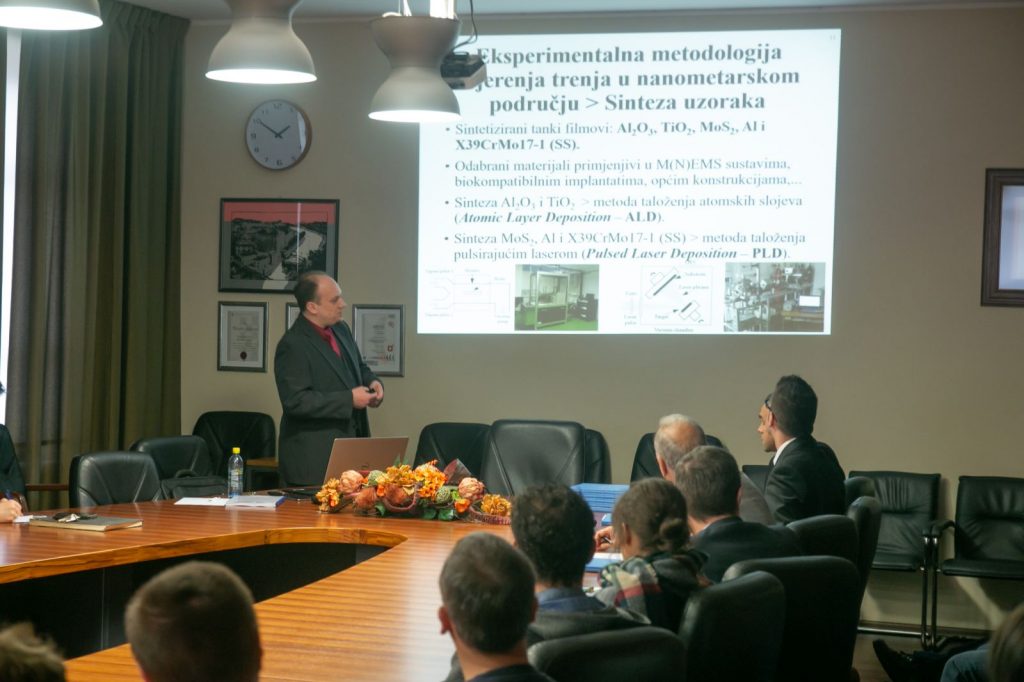
Posjet Centru za mikro- i nanoznanosti i tehnologije djece iz Dječjeg vrtića “Đurđice”
U sklopu programskog pravca 27 susjedstva u okviru projekta Rijeka Europska prijestolnica kulture (EPK) 2020., a kao inicijativa Kampus kreativnog tima Sveučilišta u Rijeci, organiziran je projekt „Čarobni dan“ gdje su se održavale kratke, kreativne i inovativne radionice iz područja znanosti namijenjene i prilagođene djeci predškolskog uzrasta.
30. studenog 2018. su tako Laboratorij za precizno inženjerstvo i tehnologiju mikro- i nanosustava pri Centru za mikro- i nanoznanosti i tehnologije posjetila djeca iz Dječjeg vrtića “Đurđice” koja su, da bi se upoznala s osnovama znanstvene metode i naprednim tehnološkim rješenjima, imala priliku otkriti što su atomi, kako i što rade 3D printeri i skeneri, što su laseri i za što se koriste, te s kakvim se uređajima za prikupljanje energije iz okoliša radi u Laboratoriju.
Završetak Moj ZABA start projekta Razvoja mehatroničkog uređaja za rehabilitaciju pacijenata sa smanjenom funkcionalnošću gornjih ekstremiteta
Završen je rad na projektu u sklopu Moj ZABA Start projekta gdje se radilo na Razvoju mehatroničkog uređaja za rehabilitaciju pacijenata sa smanjenom funkcionalnošću gornjih ekstremiteta. Kroz rad na projektu razvijen je funkcionalni prototip uređaja koji se odlikuje sljedećim karakteristikama koje ga čine znatno naprednijim od dosad dostupnih rješenja:
- prilagodljivost potrebama pacijenata i terapeuta;
- kompaktnost i prenosivost;
- učinkovitost i ekonomičnost;
- veliki rasponi gibanja uz posebnu pažnju na rehabilitaciji šake te uz veliku ergonomičnost konstrukcije;
- lagana postavka i regulacija (temeljena na National Instruments hardveru i softveru) s mogućnošću pohrane rehabilitacijskog procesa svakog pacijenta;
- omogućavanje ponovljivog, intenzivnog i visokoučestalog tretmana;
- jednostavnost konstrukcije s redundantnom sigurnošću te s laganim pričvršćenjem uređaja na ruku pacijenta pomoću ljepljivih („čičak“) traka prilagodljive duljine;
- uređaj se temelji na laganim i čvrstim 3D tiskanim dijelovima te sadrži sve potrebne elektroničke komponente;
- održavanje uređaja je lagano;
- virtualno sučelje povećava motivaciju pacijenata.
Navedeni rezultati postignuti su interdisciplinarnim radom inženjera strojarstva i računarstva s Tehničkog fakulteta Sveučilišta u Rijeci te liječnika odnosno stručnjaka na području biomedicine s Medicinskog fakulteta i KBC-a Rijeka te zahvaljujući učinkovitom korištenju dostupnih sredstava Moj ZABA Start instrumenta. Rad na ovom uređaju intenzivno će se nastaviti kroz rad kolegice Tee Arrigoni u sklopu njezine doktorske disertacije a rad će se fokusirati prvenstveno na integraciju razvijenog sučelja koje, korištenjem osjetnika napetosti mišića, omogućava detekciju željenog početka aktivacije motora, razvoj inačice konstrukcije koja je zrcalno simetrična, daljnje poboljšanje konstrukcije aktivnog sklopa namijenjenog rehabilitaciji šake, daljnje smanjenje mase uređaja korištenjem metode računalne optimizacije topologije, te relaksaciju nekih prenaprezanja korištenjem u konstrukciji podatljivih elemenata i uređaja.
Istraživačka skupina Laboratorija za precizno inženjerstvo sudjelovala na Danu otvorenih vrata laboratorija Tehničkog fakulteta
U sklopu Dana otvorenih vrata laboratorija Tehničkog fakulteta, istraživačka skupina Laboratorija za precizno inženjerstvo prezentirala je glavne aktivnosti uz naglasak na različite mehatroničke konstrukcije koje se razvijaju u našem Laboratoriju. Tom je prilikom Laboratorij obišlo 200-tinjak srednjoškolskih učenika.
Prezentacija projekta u sklopu Dana otvorenih vrata laboratorija Tehničkog fakulteta Sveučilišta u Rijeci
Razvijeni prototip uređaja, čiji razvoj je financirala Zagrebačka banka d.d., prezentiran je 23 studenog 2018. u sklopu Dana otvorenih vrata laboratorija Tehničkog fakulteta Sveučilišta u Rijeci. Tom je prilikom Laboratorij za precizno inženjerstvo obišlo 200-tinjak srednjoškolskih učenika.
Stručni posjet istraživačkom centru tvrtke Danieli
Članovi istraživačke skupine Laboratorija za precizno inženjerstvo, prof. dr. sc. Saša Zelenika (voditelj laboratorija), doc. dr. sc. Ervin Kamenar, asistenti Marko Perčić, Petar Gljušćić i Tea Arrigoni posjetili su 16. studenog 2018. istraživački centar tvrtke Danieli u Buttriu (Italija). Prof. dr. sc. Saša Zelenika održao je prezentaciju u kojoj su čelnicima kompanije predstavljene istraživačke i nastavne aktivnosti Laboratorija za precizno inženjerstvo u cilju ostvarivanja suradnje.
Prof. dr. sc. Saša Zelenika održao dva predavanja u Pazinskom kolegiju – klasičnoj gimnaziji Pazin
Prof. dr. sc. Saša Zelenika je, 16. studenog 2018.pred učenicima i nastavnicima Pazinskog kolegija – klasične gimnazije Pazin, održao predavanje „Tehnološka rješenia za pametan razvoj“ u sklopu kojega su prezentirane i aktivnosti istraživačke skupine Laboratorija za precizno inženjerstvo. Predavanje je održano na satu nastave prirodne skupine predmeta u osam razrednih odjela s ukupno 190 učenika. Istoga dana je prof. dr. sc. Saša Zelenika održao i predavanje za kolegij nastavnika i učitelja kemije osnovnih i srednjih škola Istarske županije naslovljeno “Precizno inženjerstvo i tehnologija mikro- i nanosustava za pametni tehnološki razvoj”.
3D tiskanje metalnih struktura u združenom laboratoriju LAMA FVG u Udinama
Istraživačka skupina Tehničkog fakulteta u Rijeci i Centra za mikro- i nanoznanosti i tehnologije, koja radi na razvoju rehabilitacijskog uređaja u sklopu Moj ZABA Start projekta, je 15. studenog 2018. godine posjetila združeni laboratorij LAMA FVG u Udinama (Italija), pod vodstvom prof. dr. sc. Marco Sortina. Laboratorij predstavlja sinergijsku suradnju između tri institucije: Sveučilišta u Udinama, Sveučilišta u Trstu i doktorske škole – Visoke međunarodne škole za napredne studije (Scuola Internazionale Superiore di Studi Avanzati – SISSA). Jedna od glavnih djelatnosti navedenog laboratorija je 3D tiskanje metalnih struktura koristeći aluminijske legure, titanijske legure, visoko legirane čelike, legure na bazi nikla, itd. U tom je području, stoga, razmatrana moguća suradnja. Druga potencijalna područja suradnje su u području regulacije višeosnih sustava poput rehabilitacijskog uređaja na kojem radi Istraživačka skupina Laboratorija za precizno inženjerstvo.
Stručni posjet LAMA FVG mehatroničkom laboratoriju u Udinama
Djelatnici Laboratorija za precizno inženjerstvo, prof. dr. sc. Saša Zelenika, doc. dr. sc. Ervin Kamenar, asistenti Marko Perčić, Petar Gljušćić i Tea Arrigoni posjetili su 15. studenog 2018. laboratorij LAMA FVG na Sveučilištu u Udinama (Italija). Laboratorij koji pokriva široki spektar područja mehatronike, nastao je u sklopu kolaboracije Sveučilišta u Udinama, Sveučilišta u Trstu i doktorske škole – Visoke međunarodne škole za napredne studije (Scuola Internazionale Superiore di Studi Avanzati – SISSA). Prilikom stručne posjete raspravljani su modaliteti moguće suradnje.
Održana dodjela Inicijalnih potpora Sveučilišta u Rijeci – potpora dodijeljena i doc. dr. sc. Ervinu Kamenaru
Na Rektoratu Sveučilišta u Rijeci, danas, 19. listopada 2018. održana je svečana dodjela potvrda dobitnicima ”Inicijalnih potpora mladim istraživačima za 2017. i 2018. godinu”. Događanje je bilo i prilika za razgovor mladih istraživača s rektoricom Sveučilišta u Rijeci prof. dr. sc. Snježanom Prijić Samaržijom, prorektorom za znanost prof. dr. sc. Alenom Ružićem i pomoćnikom rektorice za međunarodnu suradnju i strateška partnerstva prof. dr. sc. Sašom Zelenikom.
Inicijalne potpore dodjeljuju se drugi puta, a prvi su puta dodijeljene 2016. godine. Riječ je o financijskim sredstvima Ministarstva znanosti i obrazovanja, koje raspoređuje Sveučilište u Rijeci, a koje se dodjeljuju kao poticaj istraživačkoj djelatnosti znanstvenicima koji su na početku svojih znanstvenoistraživačkih karijera. Sredstva u iznosu od više od milijun kuna raspoređena su na 49 mladih znanstvenica i znanstvenika i njihovih istraživačkih projekata.
Uvodno se obratila rektorica: ”Naša je temeljna motivacija za ovaj susret bila razgovor i razmjena ideja. Čestitam vam na ovim potporama, za koje smo izdvojili dvostruko više sredstava nego prošloga puta. Mi danas moramo sagledati širu sliku i razumjeti da je projektna kultura nešto bez čega institucije na mogu djelovati. Znanstveni rad sam nije dovoljan, nego ne naprosto nužno da imate znanje i za vođenje projekata. Moramo biti svjesni da je to stalno natjecanje i često puno administrativnog posla. No, to nije naša specifičnost. Moramo razvijati projektnu kulturu, jer ono što nam proračun omogućuje nije dovoljno. Iako su ove naše potpore male, pogotovo kada se radi o nekim složenim i opsežnim projektima, nadamo se da vam one mogu poslužiti kao poticaj za prijavu ne kompetitivne natječaje. Hrvatska u ”povlačenju” sredstava iz Europske unije spada u tzv. ”underperformere”, a Europska komisija za to navodi tri moguća razloga: jezičnu barijeru, nedostatak motivacije i nedostatak kompetencija (ne misli se na znanstvene, nego projektne kompetencije). Mi doduše vidimo i neke druge oblike toga jaza. Druga tema koju bih željela spomenuti je pritisak na institucijama koji je na djelu kod objavljivanja i prikazivanja rezultata. Događa se da zbog takvog pritiska može doći u pitanje kvaliteta i čestitost. Gubi se supstanca pa ispada da je prilagodba sustavu bitnija od kvalitete. Bojim se da će taj pritisak sve više rasti, kao što rase i pritisak u rangiranju sveučilišta. Hrvatski prosjek koji iznosi manje od jednoga objavljenog članka godišnje po znanstveniku, zaista je nedovoljan. Danas društvo od nas znanstvenika traži više: traži se znanost pa se doda i ‘razvoj i inovacije’; traži se sve više i više. Skepticizam nas neće nikud odvesti. Moramo prihvatiti sva ta nova traženja i kritike društva, kako bismo opravdali svoje postojanje.
Prorektor Ružić pojasnio je istraživačima tehničke detalje oko administrativnih obveza iz samog natječaja te istaknuo kako će svakom dobitniku ove potpore njenim dobivanjem biti omogućeno da plati objavljivanje svojega rada, što nosi daljnje pozitivne pomake. Pomoćnik rektorice Zelenika im poručio kako ta nova znanja nažalost nemaju od koga naučiti.
Povela se rasprava oko držanja nastave, normiranja rada, količine i opisa radnih obveza, napredovanja u zvanja, pravednosti sustava, kulturi senioriteta koja kod nas prevladava… Rečeno je i kako bi možda bilo uputno dodijeliti nešto manji broj potpora, ali onda bez umanjenja sredstava, jer neki projekti bez točnog proračuna ne mogu biti izvršeni ili mogu biti ali u znatno manjem obimu i/ili kvaliteti. Rektorica je na ovo odgovorila da to uvijek jest dilema (podijeliti više manjih ili manje većih potpora), ali da se odlučuju za ovakav model, upravo kako bi te potpore služile i kao poticaj za daljnje prijavljivanje.
Može se zaključiti da se većima mladih znanstvenika zalaže za to da se projektne aktivnosti, stručni rad i rad na popularizaciji znanosti formalno boduje. Također zaključeno je kako bi bili od iznimne koristi sastanci po sastavnicama, koje bi inicirao Rektorat.
”Uz sve potpore vašim istraživanjima koje dobijete, a nadamo se da ćete ih dobiti što više, ne zaboraviti da vam je glavni pokretač vaš entuzijazam, vaša intrinzična motivacija. Mi želimo biti institucija koja će to prepoznati”, zaključila je rektorica.
Potporu Sveučilišta u Rijeci dobio je i član Laboratorija za precizno inženjerstvo, doc. dr. sc. Ervin Kamenar.
Tekst i slike djelomično preuzeti s linka: UniRi
Riječka „Noć istraživača“
Manifestacija Noć istraživača održana je u petak 28. rujna 2018. od 17 do 22 sata istovremeno u četiri hrvatska grada: Zagrebu, Splitu, Puli i Rijeci.
U Rijeci je Noć istraživača održana na 12 istraživačkih punktova, smještenih na tri kata u zgradi Tower Centra Rijeka. Riječ je o događaju koji na nacionalnoj razini koordinira Ministarstva znanosti i obrazovanja RH, dok u Rijeci u ulozi organizatora njegovu provedbu omogućuje Sveučilište u Rijeci. Događanje je dio šireg projekta – Techno-Past Techno-Future: European Researchers’ Night sufinanciranog sredstvima programa Europske unije za istraživanje i inovacije Obzor 2020.
Cilj projekta je promoviranje znanosti, znanstvenog rada i istraživanja kroz popularne oblike i aktivnosti kako bi se najšira javnost mogla upoznati sa znanstvenim metodama i rezultatima rada. Jedan od ciljeva ove akcije jest i senzibiliziranje mladih i djece za znanstvenu djelatnosti te poticanje njihovog interesa za znanost od malih nogu.
Jedna od postaja riječke Noći istraživača je bila i ona Tehničkog fakulteta i Centra za mikro- i nanoznanosti Sveučilišta gdje su posjetitelji mogli upoznati s tehnološkim rješenjima za Pametnu Rijeku, a posebno s time kako radi 3D skener, što su mikrokontroleri te pobliže upoznati lasere i vidjeti kako se oni mogu primijeniti u svakodnevnom životu, ali i kako prikupljati energiju iz svoje okoline i pretvarati je u struju. Na toj vrlo posjećenoj postaji su publici svoje znanje, uređaje i rezultate rada predstavili Saša Zelenika, Ervin Kamenar, Marko Perčić, Petar Gljušćić te student Nino Dujmešić.